Emerging U.S. Floating Offshore Wind Segment
By Philip Lewis, Research Director of Intelatus Global Partners
The U.S. offshore wind sector is laying the foundations to become one of the largest floating wind markets globally by the end of the decade, but significant challenges still remain.
The drive to grow the U.S. offshore wind sector into a leading offshore wind market continues.
The foundations are firmly in place to support the deployment of 30 GW of offshore wind by 2030 and 110 GW by 2050. Intelatus’ forecast accounts for close to 70 projects that will install around 74 GW of capacity in this and the next decade and a total 110 GW by 2050.
Within the forecast, Intelatus identifies five demonstration and pilot arrays situated off both Atlantic and Pacific Coasts for over 250 MW which are the precursors to over 13.5 GW of floating wind project capacity to be deployed in the Pacific, North and South Atlantic, and the Gulf of Mexico between 2023 and 2035. Over $40 billion of capital will be invested to deliver these projects.
Intelatus’ forecast is consistent with the targets of federal agencies, which have launched a series of initiatives to deploy 15 GW of floating wind capacity by 2035.
Further, and to support the California Energy Commission planning goals to deploy 2-5 GW of offshore wind by 2030 and 25 GW by 2045, BOEM recently launched the auction process for five 33-year leases with the potential for more than 4.6 GW of floating wind offshore California. The first capacity will come onstream at the end of this decade at the very earliest.
Despite the significant opportunities for both domestic and overseas suppliers and contractors, many challenges remain to be addressed to realize the opportunity. One area of particular concern is a potential lack of large anchor handlers required to install floating wind farm moorings and substructures.
Key differences between floating wind and bottom fixed wind projects
Floating wind projects bring a different philosophy than that seen in bottom-fixed projects. In bottom-fixed projects, the steps generally occur sequentially – components are manufactured in bulk and installed in multiple units at a time. In a floating offshore wind project, the steps will occur in parallel to allow installation to be completed in a timely manner.
Many elements of a floating wind farm resemble a bottom-fixed project. In particular, turbines and export cables are more or less the same. The foundations, array cables, and installation represent three major differences. This is reflected in the breakdown of CAPEX for both types of projects, shown for a typical U.S. project in Exhibit 1.
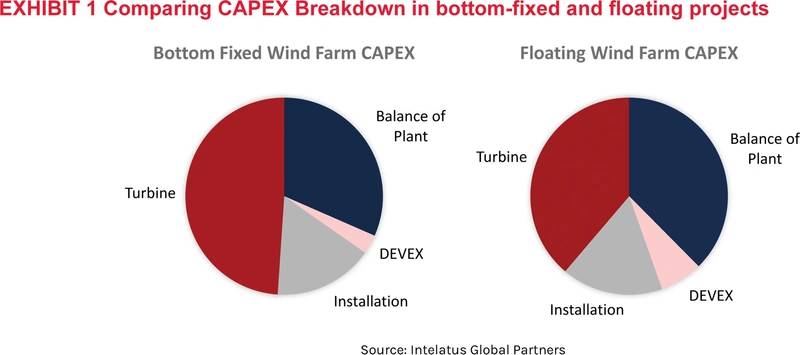
Floating wind project foundations feature anchors embedded in the seabed, mooring lines connecting the anchors to the floating substructure and the floating substructure that supports the turbine.
Currently, Intelatus’ is tracking more than 80 floating wind substructure design concepts globally, many featuring different manufacturing solutions.
The common thread of the technologies is that they generally feature physically large and heavy substructures. The concepts can be largely grouped into four main technologies, as shown in Exhibit 2. All four may feature in U.S. projects:
A more detailed look at installation requirements
Irrespective of the concept, the installation of a floating offshore wind project can generally be broken down into four major steps:
-
Mooring pre-installation. Anchors and mooring lines are installed up to a year before the turbine is installed. Mooring systems fall into two general categories. Tension leg moorings feature vertical tendons anchored with driven or drilled piles or suction anchors. Spread mooring features three sub-categories, catenary, semi-taut, or taut lines.
These systems are commonly anchored with drag embedment or suction pile anchors. Till now, catenary mooring has been commonly deployed with spar and semi-submersible structures, although semi-taught mooring will be deployed on a handful of projects in the coming years. Mooring lines will generally feature a combination of steel chain, steel wire and synthetic fiber rope. Due to the weight of moorings and the water depths for anchor installation, the anchor handling vessels deployed to install the turbines are amongst the largest in the world, as seen in Exhibit 3.
Exhibit 3 above shows the average size of AHTS used for floating wind mooring pre-lay is over 25,000 horsepower or 280-300 tonnes bollard pull. AHTSs in this range will feature back decks of over 775-800 square meters.
There are currently around 80-90 active AHTS with over 20,000 horsepower globally. If we focus only on 25,000 horsepower and above, the number falls to 24. This is an immediate concern. There is currently only one U.S. flag AHTS with over 25,000 horsepower and a further two with over 20,000 horsepower.
The 800 square meter back deck is an important guide to mooring system carrying capability. Around eight drag embedment anchors, three suction anchors, or piles can be typically accommodated on an 800 square meter back deck
-
Once moorings have been pre-laid, structures can be towed to site.
-
Electrical cable installation: Export cables will likely be mostly static high-voltage cables installed by traditional large offshore wind cable layers. The array cables and an element of the export cable are likely to feature dynamic electrical cables, which will be generally laid by modified cable layers, subsea construction vessels, and MPSVs from the oil & gas fleet.
-
Hooking up of the floater to the pre-installed moorings and array cables has been undertaken by medium and large AHTSs or MPSVs. On a large commercial floating wind farm, it is likely that both AHTSs and MPSVs will be required.
At the same time as commercial-scale floating wind farms emerge in the U.S., Intelatus anticipates large floating projects to be deployed in the UK, Europe (North Sea, Atlantic, and Mediterranean), Japan, South Korea, Taiwan, and other emerging markets.
Projects developed in these countries will be competing for a limited large anchor handling vessel and crew pool. The fleet of vessels is significantly reduced further if the weighting of offshore wind developer low and zero carbon drivers is amplified.
The opportunities are significant, but so are the challenges.
For more information about the Intelatus Global Partners U.S. Offshore Wind Report, www.intelatus.com or contact Michael Kozlowski at +1 561-733-2477 or Philip Lewis at +44 203-966-2492
About the Author:
Philip Lewis is Director Research at Intelatus Global Partners. He has extensive market analysis and strategic planning experience in the global energy, maritime and offshore oil and gas sectors. Intelatus Global Partners was formed from the merger of International Maritime Associates and World Energy Reports.