Tech Feature
Remotely Operated Vehicles
The Rise of Electric Work Class ROVs
In this article, we look closely at the latest developments in the work class ROV space. Based on what we’ve gathered, the future is increasingly electric.
By Bartolomej Tomic
Saab Seaeye eWROV
©Saab SeaeyeSaab Seaeye eWROV
If you're a regular Offshore Engineer/OEDigital.com reader, Saab Seaeye is a company requiring no introduction. Saab Seaeye’s vision of an all-electric future for underwater robotics led it to pioneer a wide range of systems that include powerful work robots such as the Seaeye Panther, Seaeye Leopard, and now its new, full-size work class vehicle, the Seaeye eWROV, along with an all-electric work-class electric manipulator.
“As the world’s largest manufacturer of electric underwater vehicles, Saab Seaeye sees a future where electric robotics perform all tasks in the underwater domain, including those currently undertaken by hydraulic systems,” Saab Seaeye told Offshore Engineer.
“It was the Seaeye Panther and Leopard that opened the market for electric work systems that could carry out a significant amount of tasks traditionally undertaken by hydraulic systems, yet offer greater precision and reliability - and are an environmentally responsible alternative,” the company said.
According to the comapny, compared to a hydraulic ROV, the 3000-meter rated Leopard is typically 50% more efficient, 30% more compact, and 50% lighter, boasting unrivalled power-to-weight ratio.
“Indeed, it is the most powerful electric robot of its size in the world,” the company says.
According to Saab Seaeye, operators of Panther and Leopard benefit from smaller umbilical cables and handling systems, smaller deck load requirements, smaller deck footprint, smaller vessel requirements and smaller transportation and mobilization needs, reducing operating costs considerably.
“They are easier to operate and maintain, more agile and responsive, acoustically quieter and more eco-friendly. The success of all Seaeye work systems sees them deployed globally for a wide range of work tasks, that can include survey, IMR, construction, drill support and decommissioning,” Saab Seaeye said.
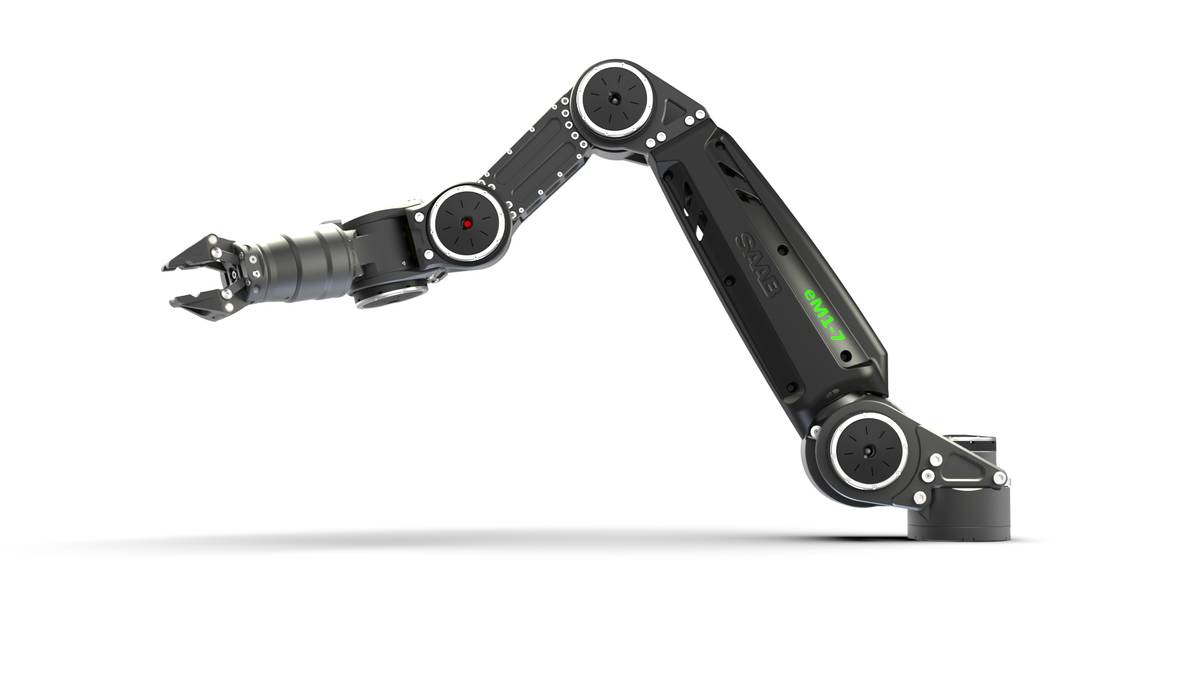
Saab Seaeye has recently developed a new system; the powerful electric work class Seaeye eWROV with an overall power and performance that exceeds that of a typical 250 HP vehicle.
In addition to what the company says are “significant advantages of electric over hydraulic the new Seaeye eWROV offers other key benefits.
Saab Seaeye says that the eWROV has been designed for onshore control for resident or unmanned vessel operations and will play an important role in future autonomous vessel fleets that will empower progress towards a sustainable future.
Designed to remain at sea for long durations eWROV can operate in either manual mode or supervised autonomous mode with human oversight and incorporates upgrading capability for increasing levels of autonomy and automation as technology evolves over time, Saab Seaeye explains.
The also stresses that electrification improves reliability and increases the mean time between failures (MTBF) thereby increasing levels of persistence and ultimately lower through-life operating costs.
“At the core of Saab Seaeye’s future-flexible robotics vision is their intelligent distributed control architecture that enables easier adoption of evolving technologies,” the company says.
During operation, the vehicles provide the operator and pilot clear and enhanced information while independently managing each device on the vehicle, including auto redundancy to keep the vehicle working even with multiple equipment damage.
Also, Saab Seaeye says eWROV has been designed with eco-responsibility in mind, with a significant reduction in carbon emissions.
Its greater efficiency and a need for less energy, results in a significant decrease in CO2 emissions overall which, combined with an electric system that has minimal oil volume, makes eWROV a significantly environmentally friendly option,” the company said.
Furthermore, the eWROV is fitted with two Seaeye eM1-7 seven-function all-electric work class manipulators.
The company says the manipulators are as powerful as a hydraulic equivalent, but more reliable and dexterous with millimeter precision and “extremely accurate” force and position feedback with each joint having its own intelligent microprocessor for intuitive and precise arm control.
Saab Seaeye said that the future would see significant growth in onshore controlled operations with vehicles deployed from subsea docking stations, or lightly manned, or unmanned vessels, where reliability and reduced maintenance will require all-electric robots for long-term deployment underwater.
“This requires increasingly intelligent robotic systems offering ever higher levels of operational capability, reliability and maintainability.
Saipem’s Hydrones
Italian company Saipem is known mostly for its large offshore construction and decommissioning vessels, pipelayers, drilling rig services, as well as for the construction of offshore production facilities. But it also develops ROVs and subsea drones.
In 2017, Saipem resolved to invest into a new generation of subsea robotics solutions and developed a program to enable new ROVs for subsea inspection and intervention.
Come late 2021, the first intervention drone, named Hydrone-R, was fully qualified and ready to go on a ten-years contract for a major operator offshore Norway.
Saipem is not resting on its laurels and is working on the next frontier of all-electric WROV, called Hydrone-W which combines high power, high efficiency, and unique capabilities as to station keeping and manipulation. This is planned to be commercialized late this year.
Hydrone-W is an all-electric Work Class ROV capable of working as a subsea resident vehicle tethered to a subsea base as well as in traditional ROV mode.
It is designed to be fully remotely controlled from the topside offshore or from an onshore control center. The Hydrone-W may also support the subsea construction activities carrying out tasks relating to construction, pre-commissioning, and commissioning of underwater infrastructures.
Hydrone-W is a 180 kW ROV said to be able to perform under the most difficult conditions. This ROV is also said to be equipped with a “revolutionary” propulsion and power management system to reduce energy consumption during operations.
It can be configured according to customers’ requirements with bespoke accessory instruments and functions.
Main Characteristics: All-electric WROV (Work-Class Remotely Operated Vehicle), 3,000 mwd rated, full DP, 175 kW, heavy-duty, capable of interfacing & handling 2-tonne skids.
In 2019 the company secured a 10-year contract with Equinor for the use of Hydrone-R and Hydrone-W in the Njord Field development.
The scope of work encompasses ROV and UID services to support drilling activities, as well as the entire plan of inspections and interventions on the Njord subsea assets (such as Pipeline End Manifolds (PLEMs), flowlines, umbilicals, and riser bases, etc.).
Control of Hydrone-R and Hydrone-W will be ensured from both the floating platform Njord-A, which recently returned to its offshore location after an onshore revamp, and from shore via Sonsub’s proprietary remote-control technologies.
Hydrones are designed, created, and developed by Sonsub, Saipem's subsea technology and equipment development center. Worth noting, Sonsub is understood to be working on the qualification of new materials and components in order to extend operability down to 6,000-m water depth.
SMD – Quantum EV and Atom EV ROVs
SMD is a subsea technology company that has been developing work-class ROVs for over three decades.
For 2023, the company’s latest products are the electric Quantum EV and Atom EV ROVs which are more compact than previous generations, help reduce CO2 emissions, and can even operate autonomously when equipped for that.
According to SMD, Quantum EV is a 270hp heavy construction vehicle with a high payload and powerful thrust output. Atom EV is a 130hp light construction vehicle suited to shallow-water, high-current work in offshore renewables.
“Both vehicles are more compact than previous generations, so they will fit on smaller vessels or uncrewed surface vessels to help reduce CO2 and cut client costs,” SMD said. SMD says the new electric vehicle range is bristling with new tech, and tech with a purpose, at that. The ROVs feature a new DC power transmission system that is said to be far more efficient and environmentally friendly than previous generations. Further, the ROVs employ advanced flight control computers to help do operations faster and maintain control in arduous conditions – such as high currents, SMD explains.
The flight control system can also link to other SMART systems unlocking autonomous functionality. They use unique electric propulsion technology that offers extreme performance in fast-moving water but not at the expense of fine control. “All this adds up to a range that can work where current generation vehicles can’t, that opens up the operating weather window and delivers higher quality results. All while being more environmentally friendly,” SMD says.
Looking to the future of work class ROVs, SMD said: “Work Class ROVs are a multipurpose tool. And as with any tool there is always a focus on how well it does the job, its reliability, and its dependability. But the offshore energy mix is changing. And we are also seeing changes to the way people work (and go to sea) with much more emphasis on work-life balance and the environment. So the robotic tools that construct and maintain energy infrastructure need to evolve.
“In the future, the tools we today call Work Class ROVs will need to be suitable for uncrewed vessel and resident work, we may see less cabled connections to the surface and onboard power systems, we will probably see AI start performing tasks, with a move from person in loop to person on loop – command to control. It will be easier and faster to undertake tasks and see the results - with real-time information at the fingertips of stakeholders anywhere in the world.”