Decarbonization
Future Fuels
Meeting the demands of the energy transition with Methanol-powered Hydrogen
By Dave Edlund, Founder and CEO of Element 1
Decarbonization is no longer a choice for oil and gas giants. Shareholders, regulators, and the public – who represent the end users of their products – have set an irreversible course towards zero-carbon economies. Yet despite the increasing pressure from the public, this journey will take time, and the energy transition represents a new tightrope to walk for supermajors and national oil companies trying to secure their post-carbon-neutral future.
The energy transition has provided the context for landmark oil and gas company funded green energy projects. Yet, even as renewable capacity expands, oil and gas will remain part of the global energy mix for years to come. This difficult balance will make it increasingly important for energy companies to make sure that the hydrocarbons they extract have the lowest possible lifecycle emissions.
The remote project problem
The most profitable oil and gas projects are often in remote or offshore locations. This naturally creates operational challenges, and grid power infrastructure is usually underdeveloped or non-existent. Yet, energy extraction requires electricity – to power vital equipment, and make staff comfortable.
Grid infrastructure can be prohibitively expensive to build in these locations, or – where offshore or in places with particularly challenging geography or geopolitics – virtually impossible to build and justify. Now, energy operators overcome this challenge with large diesel generators, which only exacerbates emissions. In UK waters alone, oil and gas emits 13.1 MM metric tons of carbon dioxide equivalent. On-site power generation accounts for the bulk of these emissions, alongside significant air pollutants like NOx, SOx, and particulate matter.
Replacing diesel generators with renewable alternatives sounds like a quick win for energy operators. However, conventional renewable energy may in itself be impractical in these areas; often environmental issues can lead to inconsistent power generation and premature wear, and getting specialist engineers on site for repairs can be difficult.
Methanol-based hydrogen generation can have an immediate impact. By using existing logistics chains and storage infrastructure, it can enable lower-carbon-intensity oil extraction, today.
Practical green energy
Most green fuels require dramatic new infrastructure. Many biofuels are more corrosive or volatile than traditional fuels and require special infrastructure for storage, shipping, and transfer. On the other hand, compressed hydrogen and ammonia must be stored at elevated pressure, necessitating heavy, bulky, and often expensive cylinders.
Liquefied ammonia and compressed hydrogen have lower volumetric energy density compared to diesel fuel. This exacerbates the logistics of transporting and storing these alternative green fuels.
Methanol does not have these problems. It can be shipped, transferred, and stored using conventional infrastructure. Methanol is not a compressed or liquefied gas; it is a liquid at room temperature. Indeed, there is already a well-developed global methanol supply chain infrastructure – using liquid chemical tankers, rail cars, fuel trucks, even steel or plastic barrels.
Using the existing methanol infrastructure represents clear logistical benefits over other alternative fuels. However, methanol has its own drawbacks as a fuel; when burned in engines, emissions of NOx, formaldehyde, and formic acid are still of concern. Hydrogen on the other hand, when used in a fuel cell to create electricity, avoids these harmful emissions.
This dynamic highlights the practical benefits of on-site hydrogen generation, using methanol as a feedstock.
Methanol based hydrogen generation
Methanol is converted into a hydrogen-rich product gas through a simple and commonly known chemical reaction. However, that process alone cannot deliver hydrogen of suitable purity for direct use in low-temperature fuel cells.
Element 1’s pioneering purification technology uses a unique membrane-separation process to deliver high-purity product hydrogen. This has made the process – and the logistics benefits associated with methanol-derived hydrogen generation – a commercially viable reality.
Multiple Element 1 membrane modules, each roughly the size of a tissue box, are paired with a compact methanol reforming reactor to produce enough hydrogen to drive a 150-kW fuel cell.
As oil and gas producers try to strike a delicate balance during the energy transition, they clearly need options to reduce the emissions associated with hydrocarbon extraction today. Methanol and hydrogen can meet this challenge, and deliver cost-effective and rapid emissions reductions, now.
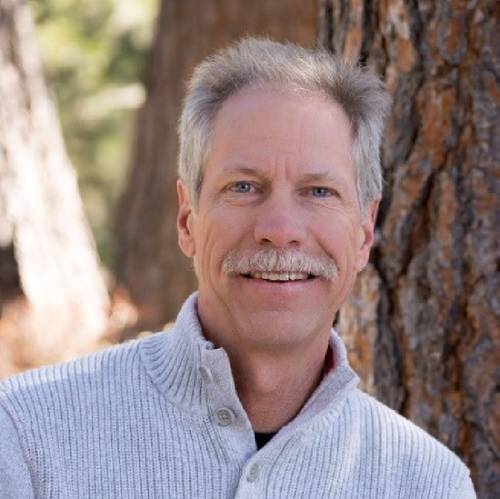
About the Author:
Dr. Dave Edlund is the co-founder and CEO of Element 1, headquartered in Bend, Oregon, USA. Dr. Edlund graduated from the University of Oregon in 1987 with a Ph.D. in chemistry, and has worked developing fuel cells, hydrogen generation technology, and hydrogen purification membranes for 35 years.