Feature
Decommissioning
A Laser Focus on Underwater Cutting
Underwater laser cutting has long been on the wish list of decommissioning project managers. The technology is now closer to commercial application.
By Elaine Maslin
The Claxton and University of Aberdeen development team. Prof Richard Neilson on the far right and Dave MacWilliam, VP Technical Solutions, at Claxton far left.
Image courtesy National Decommissioning CenterSince the development of the first functioning laser in 1960, much has been made of laser technology across science and industry, from laser-based spectroscopy to Lidar (Light raDAR) and, as a fairly standard method for cutting steel. It’s also been on the offshore decommissioning wish list to aid the removal of platforms and substructures, much of which is underwater.
Decommissioning can require a lot of cuts. For example, when it was removed in the late 2000s, the Northwest Hutton facility required more than 240 cuts, carried out with a range of tools, including massive shears, diamond wire cutters, and abrasive water jet cutting, involving a lot of mobilizing of kit and use of consumables – such as diamond wire and abrasives – all of which involves a not insignificant amount of equipment mobilization and logistics.
A project by the UK’s National Decommissioning Center (NDC), a partnership between the University of Aberdeen and the Net Zero Technology Center (formerly the Oil & Gas Technology Centre), facilitated and match funded by engineering services firm Claxton Engineering, is hoping to make some of this work easier with the use of laser cutting.
15kW of high power laser
The project takes forward an earlier initiative supported by operators bp, Shell, and ConocoPhillips through the Industry Technology Facilitator (now part of the NZTC). Now, under the first phase of the NDC project, Claxton and NDC have built and open-water tested a prototype using a 15kW high power laser – one of the most powerful industrial lasers of any academic institution in the UK – thanks to Scottish government funding.
Prof Richard Neilson, director of the NDC, says that there has been some laboratory-based work done in this space already, notably by the UK’s The Welding Institute (TWI) and by FORO Energy in de-watered environments. However, the open water trials that have been undertaken are unique.
At the time of the Northwest Hutton decommissioning, the predominantly available industrial laser for steel cutting was a gas-laser (CO₂ was often used as a gain medium to generate the laser light). Less cumbersome solid-state lasers, which often use crystal or doped fiber as the gain medium, then became more available, offering an easier-to-use system with higher power output and a smaller footprint. However, cash to access to high enough power solid state lasers has been a challenge to developing a commercial system.
With its laser and the help of the university’s optics expertise and Claxton’s subsea engineering (including developing a control system and building motors), it’s now built a system. The complete system comprises of an IPG YLS-15000 solid state Ytterbium fiber laser, which uses fiber optics, a collimator – a device that changes diverging light from a point source into a single parallel beam – in the cutting head, followed by a focusing lens and 45 degree mirror, to be able to deliver laser cutting from outside or inside tubulars. The system, which is almost neutrally buoyant, also includes an umbilical to deliver a gas jet at the cutting head, power, control, and a camera feed line.
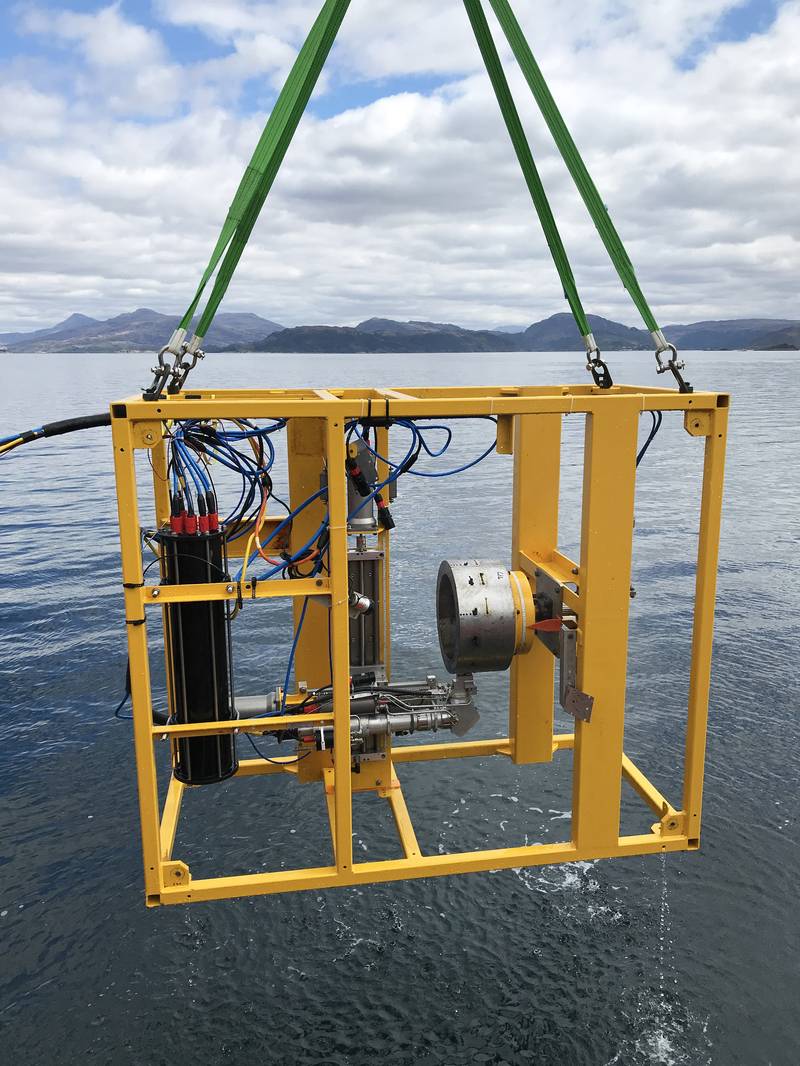
The underwater laser cutting the test rig being recovered after subsea cuts performed with the laser firing upwards.
Tank testing up to 120 mm cuts
Development and initial “Phase one” testing was done at the NDC’s facilities near Aberdeen from February to March 2021. All the components were tested to 500m-deep using the NDC’s own pressure chamber, then, using a test rig, 100 mm-thick tubular steel was cut in a test tank. The thickest cut was of 120mm thick steel, however, most of the cuts were between 40-80 mm, with an average 20 seconds to penetrate 60 mm. Next, tests cutting 60 mm-thick steel was carried out in 70 m water depth in Loch Kishorn, on Scotland’s west coast.
Abrasive water jetting could be similar speed on the same wall thickness, but the laser uses a quarter of the power requirement and a smaller deck spread, points out Prof Neilson. Being able to cut to 100 mm also means that most steel on offshore structures could be cut, he says; 50-55 mm cuts would suffice for most steel structure members, while the jacket legs on Murchison, one of the larger platforms decommissioned to date, were 85 mm thick, he says.
The test rig being recovered after subsea cuts performed with the laser firing downwards.
“Nine times faster than diamond wire”
“We’ve proven in phase one that it’s about nine times faster than diamond wire and overall cheaper than abrasive water jet cutting,” says Dave MacWilliam, VP Technical Solutions, at Claxton. He also says it’s a lower emission solution, thanks to being fully electric, which also means there’s greater control and diagnostics functionality. “There’s also a reduction in consumables,” he says. “Diamond wire uses diamond wire; if you’re cutting a jacket, the chances are you’re going to have to return to the surface many times to replace the wire. That’s non-productive time.
“Abrasive water jet cutting involves shipping abrasive materials such as garnet globally. That garnet is mined in India, the US, Thailand, and Australia and shipped around the world, so there’s cost, logistics, and emissions associated with that. You also don’t need people running around filling a hopper. Laser, on the other hand, doesn’t use any consumables. You just need two people and a computer for control. You don’t have such large equipment, it’s more agile and much more efficient – at least 25% more efficient in terms of energy use.”
The next step of the project is to undertake a real-world trial. That’s expected to happen within the next 18 months, with discussions with operators underway, says Prof Neilson.
“Our view is that it’s not going to replace all these technologies, it’s going to supplement them and will be useful in certain applications where you’re looking for agile deployment,” says MacWilliam. “Because it can be more computer-operated, rather than hydraulically controlled; i.e. people turning valves. That means it also has the potential to be deployed by remotely operated vehicles (ROV). It’s something we could use for floating production system decommissioning, where there’s a potential for multiple quick cuts, without setting a bunch of different equipment; mooring chains, flexible risers, etc.”