Feature
Deepwater Drilling
The Total deepwater roadmap
Total is the world record holder for deepest water drilling, with Raya-1, drilled in 3,400 m water depth off Uruguay in 2016. This year, it expects to break that record, with the Ondjaba-1 exploration well in 3,628 m water depth, offshore Angola. Elaine Maslin spoke with Total's Jean-Benoit Laudet and Eric Meyer about the future deepwater production systems that fields this deep will need.
By Elaine Maslin
Total's subsea oil field vision.
Image from TotalTotal is no stranger to deepwater production technology. Over the years, it's been working on some of the key elements of the future deepwater production system, not least subsea processing, and electrification.
The company has been putting electric equipment on the seabed since 2008, when it installed all-electric subsea trees in the Netherlands. It's pioneered subsea separation, with the Pazflor subsea gas-liquid separation system installed in Angola in 1,200 m water depth back in 2011.
A new phase in the subsea production system could also now be coming, thanks to a few more pieces of the deepwater production system puzzle falling into place, subsea power distribution being a key one. "Electrification will help for a number of reasons," says Jean-Benoit Laudet, Manager of the Development team within the Deep Offshore R&D Program. It simplifies the subsea system, having a grid into which production systems can plug, but it also means the ability to use renewable power, so that emissions from the upstream process can be reduced, and even disappear when the grid is 100% renewable. It also helps to improve recovery rates and makes the system more efficient, he says, when combined with moving processing closer to the wellhead.
Two deepwater visions
But first, let's take a step back. Total's over-arching deepwater vision has two routes, explains Eric Meyer, R&D Deep Offshore Program Manager. Both routes involve electrification. The first is subsea to shore, which Total has already done, albeit with an electro-hydraulic system, at Laggan-Tormore; a 140km subsea tieback in the UK North Sea, north-west of the Shetland Islands.
The second is an unmanned floating production system, powered from shore or a local renewable source, such as offshore wind.
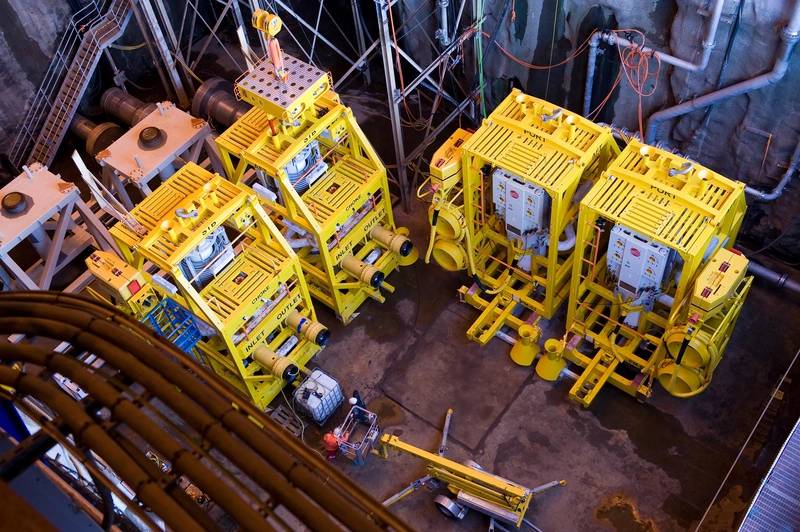
For deepwater oil fields, most of the technology required is ready, says Meyer. Subsea separation was implemented on Pazflor. "Subsea pumping and boosting is also there," Meyer says, although the company is keen for more competition in the market.
And other technologies are ready to be deployed as eXtree, Subsea power distribution (incl. VSDs) and SPRINGS, (Subsea PRocess and INjection Gear for Seawater), a subsea seawater treatment and injection unit being jointly developed by Saipem, Veolia & Total, is due to be fully industrialized/qualified by the end of this year.
For deepwater gas fields, most of the building blocks are there. Subsea compression has been proven on the Åsgard field offshore Norway (Equinor operator, Total partner), and is being implemented at Ormen Lange (Shell), also in Norway, and on Chevron's Janz-Io project in Australia, highlights Meyer. Subsea chemical storage and injection is being jointly developed by Total and TechnipFMC; TechnipFMC has developed the storage system, while a subsea chemical injection pump is expected to be trialed in 2022.
All-electric systems to support both oil and gas projects are also now largely in place. Total has been using electrical trace heated (ETH) pipe in pipe for flow assurance (on the Islay tieback in the UK North Sea in 2012), and ETH single wet insulated pipe is coming, says Meyer.
The Pazfloor subsea system, including separation.
Electric building blocks
Total installed the first all-electric subsea trees in 2008 (K5F1 and K5F2 in the Netherlands), followed by an all-electric tree and downhole safety valve (DHSV) on K5F4 in 2016.
Total is part of joint industry projects (JIPs) in Norway with TechnipFMC and Aker Solutions to develop electric actuators (with battery back-up instead of mechanical springs) and associated control system, which should soon be able to be included in electric subsea tree tenders. Total is also preparing two JIPs in Brazil, supported by ANP, to use these new electric actuators on a new generation of compact electric subsea trees. It's also in a JIP with OneSubsea, also working on electric actuators and next-generation compact eXTree in Brazil.
A further building block – the keystone, if you like – is the ability to power all of these systems, with electricity over long distances and in deep waters. This is also now ready, through subsea power distribution. Last year, following an 8-year joint industry project, supported by Total and others, ABB qualified a system to deliver up to 100MW power over 600km via a single cable and then distribute it to multiple users, in up to 3,000m water depth (See OE: November/December 2020). This could be used to deliver renewable power from shore or from a locally installed wind farm. It could also be used in reverse to gather offshore wind-generated electricity and export it to the onshore grid.
Saipem's SPRINGS concept
The wider subsea system
There are other technologies Total has up its sleeves, largely to support subsea architecture simplification. This includes a subsea automated pig launcher (SAPL), jointly developed with NOV and Equinor, to enable single flowlines to be used instead of flowloops. Laudet says this should be ready in 1-2 years' time. There's also work to fully understand the physics of fluid behavior, wax and hydrates, as well as welding and fatigue, so the design margins can be tighter. But it's also working on additional remediation options – including ways to remove wax or hydrate plugs without having to enter the pipeline.
"We're also working on the best use of composites in the subsea system," says Meyer. "This can be an enabler for some complex fields, to deal with corrosive fluids or to reduce the weight of the assemblies in some areas where there is high fatigue or high current."
Together with ExxonMobil, Total is working with Dutch thermoplastic composite pipe (TCP) manufacturer Strohm (previously called Airborne Oil & Gas) to qualify a high-pressure, high-temperature TCP jumper for permanent hydrocarbon service. TCP makes installation easier for jumpers for instance, says Meyer, because the metrology requirements are much less thanks to the TCP jumper layout.
Oceaneering's Freedom ROV/AUV during trials in 2019.
Robotic inspection technologies
"We will need to monitor this infrastructure, so we need resident remotely operated vehicles (ROV) or autonomous underwater vehicles (AUV), and some are being developed," he says. Total has been working with Equinor and Chevron testing the likes of Oceaneering's Freedom ROV, for example. There're others in the market, such as Saipem's Hydrone, which Equinor is due to deploy on the Njord field in Norway, and Eelume, which is due to deploy at Åsgard, also by Equinor, which has developed a standardized subsea docking station for these vehicles.
"We’re also looking at more functionality and deploying ROVs from uncrewed surface vessels (USVs),” says Meyer, and the supply chain is coming up with solutions in this space too, with Fugro, Ocean Infinity, and others working to provide fully remote, over-the-horizon ROV and AUV deployment solutions. These systems could also be deployed from the future unmanned FPSO, says Meyer, from a cage, for example.
A new framework that translates topside
In some ways, it’s counter-intuitive to simplify subsea systems, says Laudet. But once you’ve “broken the glass” of working in a deep and remote place, there’s an ability to spread equipment out, to make it distributed and modular. It doesn’t have to be compact, congested, and hard to work on, like on a floating production system (FPSO), he says.
“If you have to pull equipment out of an FPSO, it’s very complex and expensive,” Laudet says. “If you’re on the seabed and modular, it’s easier to pull out a piece of equipment and replace it with a working one and take the original to shore for repair. We really believe that deep offshore is not that much of an issue, and it actually offers a number of opportunities.” Meyer agrees. “You can have less of everything; it becomes quite lean in terms of design, so it helps to reduce the cost, footprint, and GHGs,” he says.
Having learned to do this subsea, the same ideology could be applied to the unmanned FPSO concept, says Meyer. “The idea is we try to apply the same criteria as we do to subsea design, to reduce the amount of equipment, reduce the overall weight and footprint of the FPSO, and to be unmanned,” he says. The target is to have only an annual maintenance visit, so topside equipment, like subsea equipment, needs to have high reliability. “For subsea, we are already there. Next is to try this topside.”
This would also be an all-electric solution, powered from shore or, for example, a nearby wind farm, ideally with 100% carbon-free electricity. For an FPSO, 90% of the greenhouse gas emissions are from flaring or venting and fuel gas. “If we want to reduce that by 45%, we move to all-electric,” says Meyer. “If you deal with flaring, the remaining 10% is around logistics, supply boats. If you go unmanned and visit only once a year, you reduce that dramatically as well. There’s also no hydraulics, and there’s less equipment to build, less steel. You reduce capex and the carbon footprint.”
All roads point to all-electric
All electric has been a long time coming, but Laudet thinks that the time is now right. ABB’s subsea power distribution was qualified last year, taking the concept forward a major step. Siemens is working to qualify a similar system. Work on electric actuators for the subsea tree is due to conclude at the end of this year, which means Total we will be able to put them in tenders for future projects very soon. “All-electric is now considered in all our projects,” says Meyer. This is very much on the table – lining up with the company’s longer-term plans.
“We had this vision to be ready for the first projects to be selected for all-electric subsea production systems (SPS) by 2021,” adds Meyer. “The power is available, and the trees will be available to put on the design, then all other bricks – chemical injection and storage, the automated pig launcher – they are coming very soon. All-electric makes SPS technologies almost water depth independent. It also means we have more control and lower emissions, so it ticks a lot of boxes.”
That leaves one challenge, to fight that reluctance to change we all too often see in the industry. Perhaps the drive to low-carbon production and remote operations might drive forward subsea electrification and doing more remotely with less?
ABB's variable speed drive during tests in 2019.
Top of the deepwater producers, in terms of its deepwater production volumes (classed as 400 m+), according to the Wood Mackenzie Lens tool, is Shell, followed by BP and then Total.
If we focus on 2020, the company with the most net working resources discovered in new fields, again, based on 400 m+ water depth, was Türkiye Petrolleri Anonim Ortaklığı (TPAO) (Turkish Petroleum Corporation). That’s mainly due to TPAO’s Tuna-1 (Sakarya field) discovery in 2117m water depth in Turkey’s western Black Sea; it was one of 2020’s largest finds.
In terms of ultradeep water – defined by Wood Mackenzie as 1,500 m plus – TPAO is still in the lead, followed by ExxonMobil, then Total, whose ca. 1,000 m discoveries in Suriname don’t quite make Wood Mackenzie’s ultra-deep grade, Hess, and CNOOC.