Feature
Deepwater Drilling
Drilling down deep
In the past 30 years, what we know as “deep water” has shifted from 500 m to nearer to 3,600m, with some projects targeting almost 4,000 m water depth today. The 2nd generation drillships, which dominated the field at the early stage of deepwater exploration drilling, have now been replaced by 6th and 7th generation units. Elaine Maslin spoke with Total’s Philippe Jeannet, Drilling & Wells Manager, Deepwater & Subsea Product line, about deepwater technology evolution and what’s coming next.
By Elaine Maslin
The Deepsea Stavanger semisubmersible drilling rig in the not always so calm waters off South Africa. Photo from Odfjell Drilling.
What we consider to be deep water has changed dramatically in Philippe Jeannet’s career. When Jeannet started in the business 30 years ago, on the Pelican class drillships, above 500 m was considered deep.
Today, the industry is drilling in close to 3,600 m water depth. This year, Total expects to break its own deepwater drilling record (which is also the world record), with the Ondjaba-1 exploration well in 3,628 m water depth, in Block 48, offshore Angola, using the Maersk Voyager drillship.
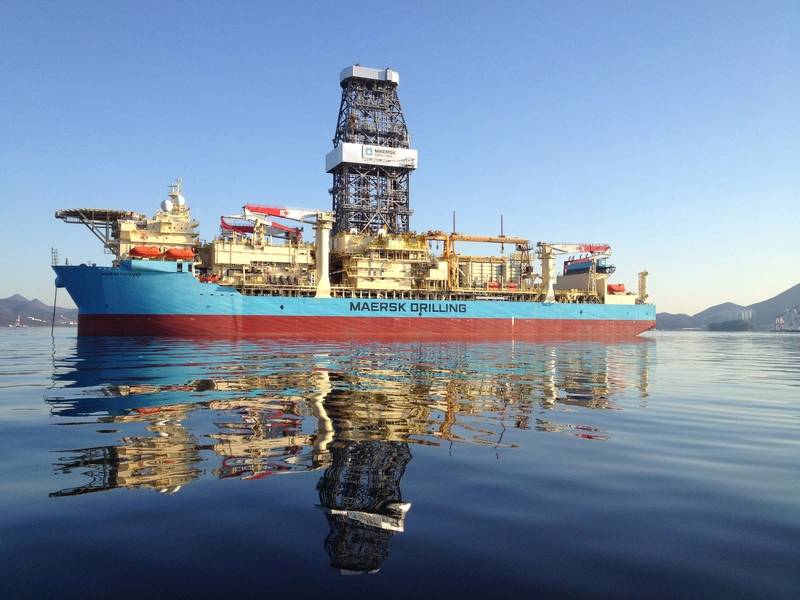
Maersk Drilling’s Maersk Voyager is lined up to drill the deepest water well ever drilled later this year, for Total.
It’s been quite a journey. There have been major advances, such as global positioning systems, which meant rigs no longer had to solely rely on an acoustic relative position derived from a seabed beacon, and the introduction of 5th generation drillships, from 1998 onwards, took water depth capabilities up to 3,000 m.
Since then, many of the advances have been incremental, such as increasing power and size has meant depth ratings have crept from 3,000m to 3,600m, with hook load rising to 2.5 million lb. from 2 million lb. on the latest 7th generation rigs without forgetting the huge improvement in the BOP capabilities and control systems since Macondo.
A soft, high-impact focus
It’s also been about automation and then digitalization, and more of that will help, said Jeannet. The first step in automation has meant that human roughnecks no longer need to be on the drill floor manipulating heavy loads. Digitalization takes that to another level, enabling more intelligent systems that can detect when something isn’t right and react, and real-time access and analysis of critical data from anywhere in the world.
At a first level, that means if you detect high torque in the drill string, the top drive will automatically decrease the rate of rotation to regulate the torque, said Jeannet.
Systems can be programmed to run soft torque operations or at an automatic rate of penetration. “This was a big area of improvement, which we’re still improving on as there are a lot of things we can do on this system.”
With real-time access to operational data from onshore, “We can follow operations in real-time, see flow rate, pressure, hook load. It’s easy to follow the operation and detect an anomaly,” said Jeannet. “More than that, you can detect a situation that’s maybe difficult to detect by a human being. With AI you can predict that the situation will deteriorate and then prevent it from happening. This is what we are developing at Total with our Drillx system.”
These techniques, combining digitalization and automation, could help reduce non-productive time (NPT), which can be up to 20-25% of operational time. “Doing what we’re doing today, without mistakes, could save part of that 20-25% lost drilling time, which is huge and which is why, today, we focus more on this than on other R&D leads, like dual gradient drilling.
“In deep water, everything is huge. The day rate cost is huge; a deepwater rig is more or less $1 million per day operation. Every hour lost costs $42,000. This is why deepwater is an enabler for these types of technology, because every hour saved has a huge impact.”
Hardware still comes into play, however. Other deepwater drilling developments have included the use of managed pressure drilling (MPD). While it’s been used in onshore and shallower water drilling for some time, using it in deepwater meant overcoming potential weak points in deepwater riser systems, i.e. the telescopic joint. That has meant adapting MPD technology so that it could be integrated into the riser below the telescopic joint. But with the ability to use MPD, pressure managed mud cap drilling could also be used, to maintain overpressure on the reservoir when there are fluid losses, and this is something Total has used, including in Mexico in 3,300m water depth.
Cleaner operations
Today, there’s also a large focus on carbon emissions reduction, said Jeannet. “6th and 7th generation rigs have 33 MW or more of power, so they’re consuming a lot of fuel.” To reduce this fuel consumption, there’s a big focus on engine management, he explains.
For redundancy, these vessels have six or eight marine diesel main engines. In normal metocean conditions, using just one or two would suffice, but redundancy is needed during drilling operations. This is why most DP3 operations use three engines across three split engine rooms. Instead, closed-bus operations are being considered where the engines rooms are connected, so just two need to be used. Peak demand periods could be supplemented with batteries, to create a hybrid system, said Jeannet.
The next big target
Despite being in record breaking water depths, no new technology is needed for the prospects Total is chasing today, such as the Ondjaba-1 prospect, said Jeannet.
North Platte drilling operations in the US Gulf of Mexico
“We are using the same technology, but making it a bit bigger and more efficient each time,” he says. But, going further than 3,600 m will start to push the limits of current systems, he says. “We are using a multiplexed blowout preventer (BOP) control system that’s still hydraulic,” he says. “If we’re to go deeper, maybe we have to bring additional technology, like all-electric BOPs, so you don’t pump any more fluid into the BOP, you just use electric power and motors, which you can use without any depth limitation.
“At some stage, you need to think differently if you want to go further,” he adds. “Today, we’re working a lot on all-electric wells. We believe we’re able to design a well which can be operated electrically.” With an all-electric well, subsea fields in deepwater will no longer need kilometers of hydraulic lines and the potential for hydraulic leaks, he says. “All-electric is a good enabler to develop subsea fields at a lower cost, and I think that we will also be able to do things we are not able to do with hydraulic.”
There’s also a push towards 20,000psi (20k) deepwater systems. Today, the ‘norm’ is 15k, and most rigs have a 15k BOP, 15k choke lines, etc. But, “today we’re developing fields where you need more than 15k, so we have to develop 20k equipment,” said Jeannet. North Platte in 1,500m water depth in the US Gulf of Mexico requires 20k systems because of the reservoir pressure. “We’re drilling below 5,000m of salt,” said Jeannet. “The vertical total depth is 35,000ft, that’s more than 10 km of well, and the pressure is very high. If you want to develop this kind of field, you need to have Xmas trees and BOPs able to handle this kind of pressure.”
Handling the Agulhas current
The Agulhas current. Credit, Oggmus, Wikimedia Commons
In South Africa, where Total has made two recent discoveries in Block 11B/12B (Brulpadda, in 1,400m water depth (2019), and Luiperd, in 1,800m (2020)), the challenges of deepwater drilling are compounded by very specific harsh ocean conditions. Drilling on Brulpadda was successful on a second attempt, using Odfjell’s Deepsea Stavanger semisubmersible, which was also used for Luiperd.
“The North is Sea harsh, but it’s because of wind and waves,” said Jeannet. “In South Africa, it’s more or less the same. But on top of that, you have deeper water and a high, 2m/sec, or 4-6 knot of constant current from the Agulhas current, which runs from Mozambique and Madagascar to South Africa. When the wind and are current together, it’s very difficult for a vessel to keep position. Sometimes the wind and current are not coming from same direction and that means you cannot optimize the position of the vessel because you still need to withstand the current.” Only semisubmersibles can be used, and due to the inability to optimize position against the current/wind and they need to be high capability, he says.
On top of that, the Agulhas current flows from the surface to more than 1,000m deep, so it makes running the BOP a challenge, with it being up to 70m offset from the rig. Only a few rigs in the world can operate in this environment, said Jeannet.
The riser system also needs to be adapted, to add in more flexibility, withstand the force of the current and to prevent the riser from colliding with the semisubmersible’s pontoons. This has meant adding a third flex joint to the riser, level with the pontoon, as well as tensioning lines, to keep it in a fixed position.