Feature
Floating Wind
Floating Wind: Through the pilot stage
It’s the eve of (another) major expansion in offshore wind. In a great push, floating wind is being handed former “deepwater” oil and gas acreage, and new wind provinces are being named. Grid-operator developers “agnostic” about their choice of turbine types are finishing up pilot projects, although new concepts are still attracting investors. A revamped supply chain — minus the jack-ups of fixed wind — is nearly ready to go. While fixed turbines go in “everywhere”, a handful of floaters are anchored in water over 60 meters (180 ft.) deep. Despite obstacles and unknowns, the ocean seems the limit for this floater segment.
By William Stoichevski
Slide-out: DemoSATH build and launch sites at the Port of Bilbao, Portugal.
Courtesy: SAITEC/RWEThe opportunities in offshore wind are well known, and the Biden Administration isn’t alone in the world if offering subsidy for turbines offshore. For three years, the International Energy Agency has hammered home the message, “It’ll become a $1 trillion industry.” How much of that will be floating wind in deep water?
About 50 billion British pounds, says Katherine Phillips, managing director of UK-based advisor to wind developers, OWC. At a talk in Norway, her words are absorbed by investors interested in the “risks and opportunities in floating wind”.
What Phillips and her hosts seem to want to make clear is that offshore floating wind may be stalled for want of coastal resources and offshore concessions. Recent floating wind pacts have been more an attempt to convey a pipeline of projects than a pledge to immediately begin building. “We believe that the next step for floating would be scale and line of sight projects to allow the supply chain to make necessary investments and accommodate standardization and industrialization,” Equinor spokesperson, Magnus Frantzen Eidsvold, tells Maritime Reporter.
Phillips makes clear that large and small pilot floater projects by the likes of operators RWE, Equinor and others are not quite the mass commercial breakthroughs investors are supposedly waiting for. Yet, a breakthrough is in the cards, Phillips implies, pending certain new design successes and an understanding of how existing wind floater concepts might not be enough. Moreover, sailing out to deepwater wind “provinces” could be more expensive, as it was with oil and gas.
In Europe, the waters off East Anglia, Denmark and northern Germany are entirely fixed wind. It’s off Scotland, Norway, France — and now Asia — where the gaggles of floaters float. Yet, while Equinor (it took 20 years) and RWE (10 years) have braved the pilot stage of floating offshore wind, other engineering players — and investors — have forged ahead and made alliances with newly interested national governments and their industrial champions. The lure of floating wind is its offering of “added value” for new and existing maritime players and, for some, a bit of energy independence.
Nearshore, then offshore
Much more in floating wind happens nearer to shore. Techniques involved in the fabrication of semisubmersible steel and concrete “jackets” — whether “tetra-spar or spar buoy” — are dependent on “a limited number of tall cranes”, reinforced quays, and, Phillips cautions, much more sheltered harbour area than one might have imagined for their storage before tow-out.
Floating wind concepts signal a move away from jack-up installation vessels that hammer down pilons and toward shore for fabrication and assembly. The pilots are largely about sorting out the build-and-float process. In fact, the turbine you see will have been entirely built dockside in a process reminiscent of Norway’s building and tow-out of its giant gravity-based, concrete oil-and-gas structures (see Troll float-out). Floating wind turbines are towed to their offshore concession by tugs and offshore service vessels, or OSVs, and anchored, not piledriven or dropped, into place.
Equinor was first mover. The company had for years been contemplating the HyWind design’s launch, perfecting its build and placement, knowing that it was a spar design familiar to offshore suppliers. By all accounts, HyWind Scotland is a success, although not, we understand, without the occasional lost anchorage or snapped dynamic cable (not the ordinary seabed-hugging comms-and-electrical cable, but a buoyant strand that reaches from surface to sea bottom). HyWind is Norway’s lead in the floating wind game. Yet, HyWind is dependent on Norway’s many deepwater ports, a major advantage, for its manufacture. “It works. The spar buoy concept is good,” Phillips says. “But If you don’t have fjords, its going to be really difficult to manufacture and install them, so I think there’s going to be limited markets around the world where that’s a really cost-effective solution.” Still, Hywind is the stuff of pilot wind parks Hywind Tampen and Hywind Scotland.
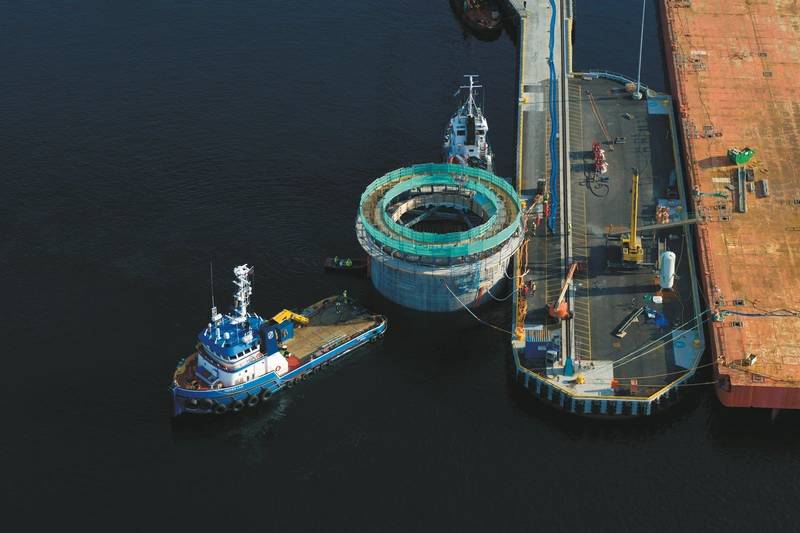
Quayside transfer of a Hywind Tampen module, September 2022.
DemoSATH
Enter RWE and its Spanish pilot, DemoSATH, now launching in the Port of Bilbao. Its load-out from quayside — an operation unique to all wind floaters — and its construction promise to do something akin to serial production via dedicated drydock, if still dependent on fortified quays. That makes it more appealing to the world’s shallow-water, wind-energy coastal base hopefuls. Like Hywind, DemoSATH is floated offshore to be connected to its pre-positioned submarine dynamic cable and mooring lines (an R&D mooring alliance already exists in Norway). Also like Hywind, the DemoSATH prestressed concrete platform is pre-assembled, and it’s 2 MW turbine can be attached within a rope’s through of its quay. Still, tall cranes seem to be required.
DemoSATH rolls onto a semi-sub drydock via self-propelled module mover and then ballasted until the turbine stem is buoyant. “Once afloat, it takes less than 45 minutes to safely berth the DemoSATH wind turbine at quay,” Araceli Martínez, chief of engineering at Saitec Offshore Technologies, is reported saying. The demo turbine is being hooked up to the Spanish grid as we write these lines. Martin Doernhoefer, director of floating wind at RWE renewables, says the operator is aiming for 1 GW of floating wind capacity by 2030. “Jointly, with our other pilot projects, DemoSATH enables us to gain early experience for our future developments.”
Scottish base
In late August, Norway-based Aker Offshore Wind made headlines for a merger with Irish floating wind developer, Mainstream Renewables, just as the latter’s partnership with Ocean Winds had produced preferred bidder rights in a 1.8 GW concession in the lucrative and expansive Scottish wind program (worth GBP 21.4 billion, or USD 23.23 billion — just under half of the coming world market for floating wind).
The Scottish wind spend, leaked by promoters and picked up by advisors OWC, dwarfs planned UK spending of GBP 6.9 on floating wind, and the GBP 15.5 the EU claims is on its way. Scotwind is said to be more than three times the current GBP 6.2 billion expected floating wind spend talked about for the rest of the world.
Mainstream backs the floater concept Windfloat from Principle Power, a Mainstream business partly owned by EDPR, EDP Ventures and Tokyo Gas. Windfloat pilots in Portugal, France and Scotland will grow to 100 MW of installed capacity by year-end. The Windfloat concept has already set a record for floating the world’s largest floaters: three 8.4 MW turbines launched from a solid-looking coast base in Portugal and commissioned in 2020 some 20 kilometers offshore Viana do Castelo.
Key to Scottish wind aims is the converted Hunterston Ore Terminal — a marine yard once used to build oil platforms and drydocks — and its availability is much proclaimed, another sign of how sorely needed coastal bases are for floating wind. In Norway, at least five bases are available to wind developers, including Coast Centre Base and Bergen. All are deepwater. All, we can attest, offer fabrication. These coastal bases are key and supplant, for now, the offshore jacking vessel.
“For serial production, the general feeling is that drydocks probably won’t be the solution in the end, but for demo projects and smaller scale development they’re probably still very useful,” Phillips says.
WindFloat
The Windfloat semisub’s benefits are on the build-side, during assembly, float-out, operations and maintenance. The design claims include an ability to mount “any” commercial turbine on one of the tetra-buoy’s three mounts. Stability plates welded to its caissons and digitally controlled hull-trim help it align with wind conditions.
The Windfloat’s modular design affords the use of truck-mounted cranes to aid in the construction of turbines, with the hire of something larger — like the 700-tonne quayside, or 3,000 t ringer cranes launched for floating wind by Netherlands-based Huisman this summer — to assemble turbine and blades on the spot. The design has attracted the interest of Asia’s wind-interested for its ability to scale in sync with turbine sizes while avoiding offshore heavy lifts.
Seaside logistics
Smaller service vessels — a tug or two, an anchor-handler — is about all a floater seem to need, although Phillips seas a potential need for “something that floats” to do turbine assembly offshore if tall-enough cranes are nowhere to be had onshore.
Apart from deep quaysides of high-bearing capacity, floating wind port builders must plan for “a large footprint for floating foundations”, Philips says, adding that while large hull forms, dry docks, specialist mooring and flexible cables mimic oil and gas builds, “You can learn but you cannot copy oil and gas.”
Principle’s Windfloat seems to have assimilated those lessons, right down to the moorings; passive ballast systems and smart hull trim to provide stability and a draft.
Fronting the Windfloat, Mainstream is planning GW-scale wind farms in Vietnam, South Korea, Japan and Sweden. In all, OWC sites 54 potential floating wind markets to watch in a report for wind-watchers.
The Windcatcher
While Phillips sites the levelized cost of energy — the largely front-end loaded price tag of ocean electricity — in floater designs, there’s one off-the-radar floater design that might have an LCOE edge.
Maritime Reporter’s conversations with wind-savvy investors (often engineers and corporate captains themselves) led us to a concept promoted by North Energy that also boasts offshore pedigree. The Windcatcher — from a distance, a Soviet-era early warning radar — is in fact “an efficient floating wind design”, especially on projected LCOE.
North Energy dropped oil in 2017 to focus full-time on projects like Windcatcher —pride of former Aibel offshore engineers and CFO, Ronny Karlsen. “The Windcatcher is a multi-rotor turbine grid that represents a new type of wind turbine,” he says, adding in an email, “The Windcatcher maximizes power generation per floating installation, which reduces CAPEX and OPEX.” A peculiar maintenance cost-saver includes a built-in elevator system that rises to allow blade or cell repairs. No specialized vessels. Already, Karlsen’s backers include General Motors Ventures in “strategic” alliance.
Karlsen points to the cubic law of science which holds that weight and cost scale disproportionately with the swinging radius of a blade, represented by the volume of a sphere. “One of the defining features of the Windcatcher is the fact that it bypasses the cubic law valid for a single turbine.
“The scaling potential for the Windcatching technology is phenomenal,” he says. “This is just the beginning.
Strategic
North Energy CEO, Rachid Bendriss, tells Maritime Reporter over the phone that the Windcatcher’s lean logistics chain looks leaner than with other floating arrays. “It’s a new way of thinking. There are serious people liking the design,” Bendriss says, adding that what they like is the low potential LCOE of a multi-prop array. Levelling costs means levelling logistics.
“The key benefit of the design is that you circumvent the whole thing about bigger and bigger turbine wings that are large enough to cover the cost of what’s underneath (as in hidden, gigantic blade-repair tow-backs and maintenance across a 200 square-km park),” Bendriss says.
For the likes of HyWind et al, it is understood that the breakeven price is about EUR 150 (USD 145.5) per MWh. “That 150 to 200 is for floating wind, and the industry needs to find EUR 50 per MWh — and CAPEX per output unit of GW hours,” Bendriss says. The main challenge with Windcatcher is “client comfort” with the multi-rotor design, or belief in its viability and buildability. “The multi-rotor concept is not new,” Bendriss adds.
Venerable design engineers at Aibel and ABB have done a feasibility study with calculations on costs versus other floaters. It’s been two years, and the Windcatcher’s time — this era of higher costs — has come.
Equinor spokesperson Eidsvold would seem to agree: “We are technology agnostic … We started out with the HyWind concept and have expanded to the Wind Semi concept.”
Shipping, construction & peripherals
In the background — all around, really — remains the offshore wind fleets, their deliverables and powerful national interests in sustaining fleets and their tech.
While the wind floater might do away with offshore construction jack-up vessels, there’s still plenty of shipping and peripherals in the floating wind ecosystem to keep wind-related shipping afloat, especially for those suppliers with experience offshore. Edda Wind, a dedicated wind service company based in Haugesund, Norway, has two offshore wind service vessels and seven under construction. “There is a strong demand growth, estimated 250-plus vessels required by 2030, excluding China. This is far exceeding existing tonnage and order book of totally 49 vessels,”
Edda Wind chief exec, Kenneth Walland, says in an investor note. As repurposed oil and gas vessels “exit the wind market”, he says, rates for Edda’s wind service operation vessels (SOVs) and (wind-park-) commissioning service operation vessels (CSOVs) “are increasing”. Cable layers, like Nexans, and even offshore heavyweight GustoMSC — of jack-up lift boat design fame — are already airing ways to help floating wind (GustoMSC is understood to have its own “lab phase” Tri-Floater semisub foundation concept for large wind turbine tested in France and qualified by DNV, as well as a new construction vessel for deeper waters).
The decommissioning of floating wind — already the subject a report for Scottish regulators by Equinor’s Hywind Scotland Pilot Park — will also offer shipping work. Equipment to be decommissioned includes the five 6 MW turbines; 15 mooring lines and 100-tonne, 15 suction-bucket anchors; 4 infield cables; 1 export cable
Floating help: The Edda Passat attending a fixed wind turbine
Asian journey
Specialized tonnage is also needed in Asia, where Equinor is in on the 200 MW and 800 MW floater farms Donhae and Firefly. Long-time Equinor supplier, Subsea 7, is one of few offshore contractors not to go bust in the early days of Britain’s wind energy story. The supplier-contractor can pencil its formidable fleet into the engineering contract awarded in late August by Corio and TotalEnergies for the 504 MW Gray Whale 3 floating wind project, 70 km offshore Ulsan, South Korea.
“The basic design contract will be executed in a consortium with Technip Energies and Samkang M&T and will include engineering of floating foundations, mooring and inner-array cable in collaboration with the turbine supplier,” a communique reads. Yes, they said floating wind.
No easy road
Once those turbines are afloat in the windiest locations, knowing weather windows for maintenance and repair operations becomes a cost-saving ability. To prevent the wasted fuel, day rates and time of crew moves cancelled due to weather, sensor technology is now available. For, at least, fixed wind, there’s MIROS of Norway, who can define wave heights. Wind conditions and the overall “spatial awareness” of a floating wind park — radar showing everything out there, surface vessels and subsea cables — is available for operators from compatriot company, Vissim.
Expect the entire oil and gas supply chain to show interest in offshore wind. California’s Humboldt Bay — now a shoe-in for floating wind after Biden’s pledge of 15GW by 2035 — will see the oil industry’s finest install at least one of the five floating concepts: semi-sub — TLP, tetra-spar, spar-buoy and multi-rotor — in a bid to get to Biden’s goal of US45 per MWh.
Disconnect
“At the moment there are only pilot projects installed in pre-commercial arrays installed around the world,” Phillips says. The biggest is HyWind Tampen with its 88 MW. “So, when you compare it to the gigawatts in fixed wind projects around the world, obviously the industry is a little behind”
Yet, supply chains are ready. They might never have replaced a blade or gearbox on a turbine in 100 meters of water, but they will never have to, as floating wind concepts all disconnect — some not as easily as others — and tow back to port.
They have time to learn. Even industry advocacy charts show a long, 10-year road to “first wind” in deepwater.
The summer 2022 tow-out of a Hywind Tampen concrete form, bottom half of the spar buoy.
About the Author:
After a honing the media campaign of Norwegian green group Bellona (current fuels advisors to the European Commission), William Stoichevski began working for the Associated Press in Oslo. In 2003, he left the AP to oversee and write for a number of print and electronic energy industry publications in the Norwegian capital. William lives and works in Oslo. He started writing for Maritime Reporter in 2014.