A new generation in motion sensing for autonomous subsea vehicles
How AUV’s are evolving and how the next generation of inertial technology will help transform performance.
Darioosh Naderi, Business Development and Product Strategy Manager at Silicon Sensing.
IMU in test at Silicon Sensing
Photo Credit: Silicon SensingIt was not that long ago that remotely operated subsea vehicles (ROV’s) tethered to a ship or other platform and controlled by a pilot were the de facto standard in the marine environment. They were the accepted solution for many tasks including ocean floor surveying, construction, research and inspection. Over the last 10 years, as technology has developed, there has been a dramatic shift to the use of completely autonomous underwater vehicles (AUV’s).
By reducing the requirement for a surface vessel to shadow the AUV, as is typically the case with ROV’s, operational costs are decreased whilst flexibility is increased. Rather than acting as the control platform for one or two ROV’s, we see increasing instances of one surface vessel acting as the base for multiple, even a fleet, of AUV’s. And without the need for a tether, AUV’s can be smaller and lighter, able to operate at greater distances, for longer and in more restricted spaces. AUV’s can become highly effective force multipliers. They are increasingly the choice for data gathering, observation and surveying activities – and the range of tasks they undertake will only grow.
Today AUV’s are regarded as mainstream technology and as this market grows and evolves it will represent a major, market-shifting opportunity for many supplier companies.
Looking to the immediate future, what do you see as the main challenges and opportunities for suppliers to this marketplace? What are the next steps?
Increasing AUV endurance is the key challenge for the future - extending how long a vessel can remain on task, how deep and far it can travel.
For this reason, the driving focus for all suppliers is to minimise both the size and power consumption of any item that will be installed on the AUV, whilst maintaining or improving performance. Any gains here will help extend battery life, allowing the vessel to operate effectively for longer periods and over greater distances.
In the inertial sphere, what has already changed as companies have begun to address this market?
Suppliers of traditional inertial technology such as fibre optic gyro (FOG)-based systems, which deliver extremely precise performance but are typically larger and less rugged than alternative technologies, are already on the path to reducing the size of their systems whilst attempting to maintain performance levels.
For Silicon Sensing, and companies focused on micro electro-mechanical systems (MEMS)-based inertial products, the focus has been at the performance end. MEMS inertial technology is well known for its compact and rugged qualities, and for its lower power consumption, but until now there has been a perception that the performance of MEMS devices is less precise. With the latest generation of products this is not the case. A number of new MEMS-based products have been launched across the market recently and these are challenging FOG performance. These include Silicon Sensing’s DMU41 9 degrees of freedom (DoF) inertial measurement unit, launched last year, and the company’s new CRH03 stand-alone gyro. Both represent viable and cost-effective alternatives to much heavier, larger FOG products.
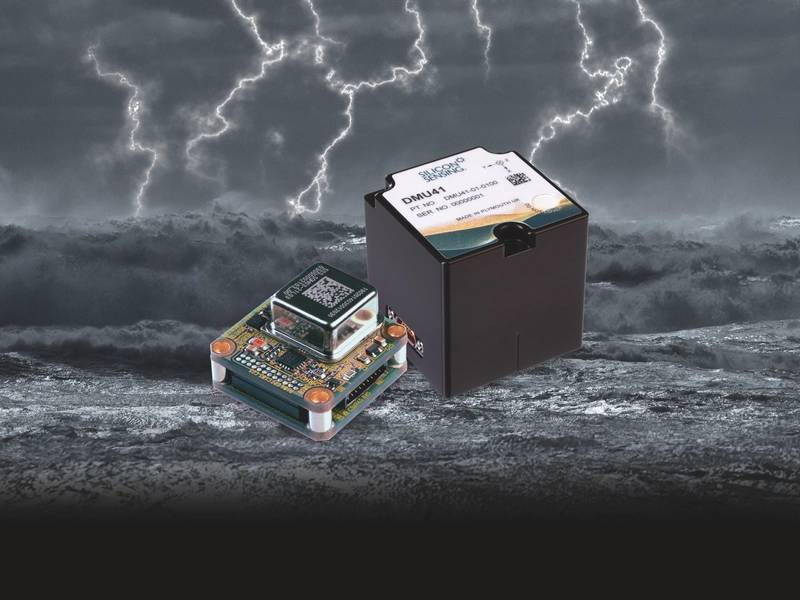
Silicon Sensing’s recently launched DMU41 IMU and CRH03 gyro
Do you face other challenges to meet this market’s needs?
For suppliers of inertial sensors and systems, such as Silicon Sensing, a prolonged time on task presents an additional and important challenge. The further an autonomous vehicle is away from a reliable external positioning source, (such as GNSS, USBL, LBL) the less access it has to reliable data to constrain any drift in its position.
As AUV endurance targets extend, the goal of the next generation technology must be to deliver longer-term navigation in the absence of external positioning sources. Effective AUV positioning over time requires inertial systems to be integrated with sensors such as doppler velocity logs (an acoustic sensor that estimates velocity relative to the sea bed). This is already industry standard practice with integrated outputs delivering accurate, drift-free positioning data.
The challenge now is to further miniaturise this integrated package while delivering the same, or better, levels of performance – and this is where MEMS inertial technology can really shine in the coming years.
How have these changing requirements impacted the shape of the market?
The huge potential uplift in demand has brought new energy to the market. The race is on to deliver a new generation of disruptive technology that delivers longer term navigation in a smaller package. There have been mergers and acquisitions as companies have positioned themselves and incorporated the technologies they require. New players have entered the market and there has been a far greater level of investment aimed at funding the innovation required to unlock these opportunities. These are exciting times in the inertial sensors and systems market.
What is next for Silicon Sensing?
Silicon Sensing is well placed in this landscape, with a new generation of technology already underway. A key goal is to deliver gyro compass-grade MEMS inertial sensors within the near future without adding more costly and heavy systems to the payload - and this is a target the company is well on the way to achieving.
Silicon Sensing already supplies MEMS products based on inductive, PZT and capacitive technologies and current development work shows very promising performance gains and size reductions with work sufficiently mature for Silicon Sensing to be exploring routes to move to production within a few years.
Silicon Sensing’s family of inertial sensors and systems
How will this solve current real-world problems and what are the main target markets?
Looking ahead, the availability of gyro-compassing and navigation-grade sensors at the MEMS size and price point will represent a landmark shift in the inertial marketplace, opening up new applications and creating opportunities that have been neither operationally possible nor economically viable with established technologies.
One of Silicon Sensing’s prime target markets is clearly subsea AUV’s but the new generation of integrated inertial navigation systems and technologies will offer critical benefits for many high-value sectors, including aerospace, space, industry and defence. In the defence arena the company envisages benefits for many vital operations, including undersea mine countermeasures and mine sweeping as well as USV reconnaissance.
The next generation of MEMS-based inertial technologies will introduce a new world of possibilities.